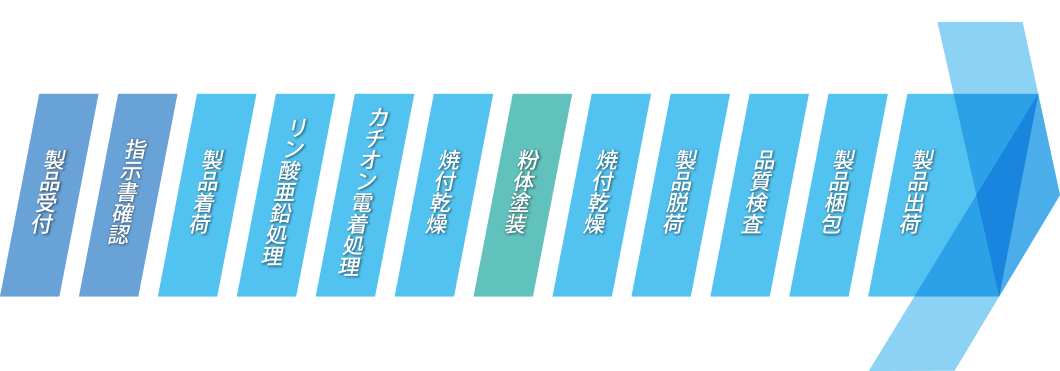
1. 前処理
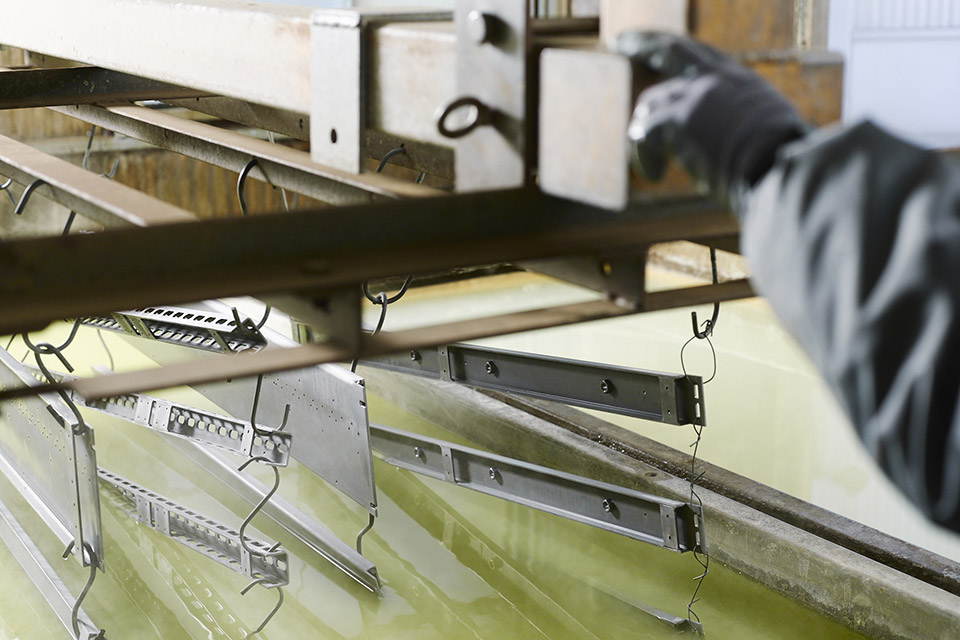
塗装の密着性を向上させるため、油成分を除去するアルカリ脱脂工程、次に錆を落とす酸洗工程を行います。被塗物表面の不純物が除去されたところで、最終工程として化成処理を行います。化成処理工程では、防錆性が高く緻密な皮膜を形成するリン酸亜鉛皮膜が塗料との密着性を向上させます。
2. 水切り乾燥
化成処理後の被塗物表面は水洗工程により濡れた状態になります。このまま粉体塗装を行うと被塗物と塗膜の界面に水分が残り、塗装後に発生する不良のひとつであるブリスターの現象が起きてしまいます。そのため塗装前に水分を除去することが重要となります。本工程で被塗物の水分を完全に除去します。
3. 粉体塗装
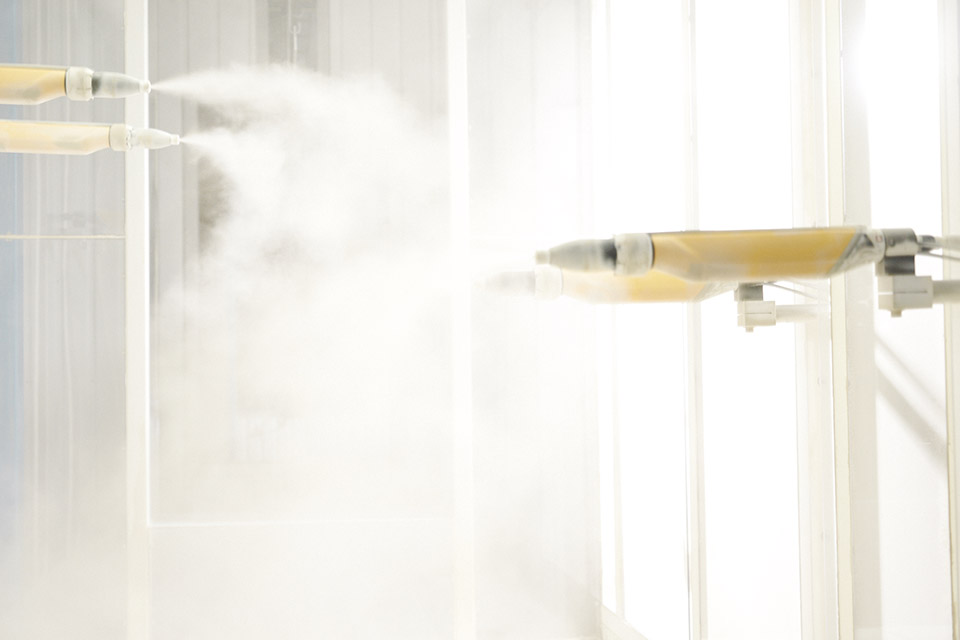
粉末状の塗料をエアーによりガン先から吐出させ塗装する手法になります。吐出する粉体ガン内にある電極へ電圧を印加するコロナ式粉体塗装、粉体塗料がガン内を通過する際の摩擦により静電気を発生させるトリボ式粉体塗装があります。1回の塗装で溶剤塗装の2~3倍の塗装膜厚を得ることが出来ます。
4. 焼付乾燥
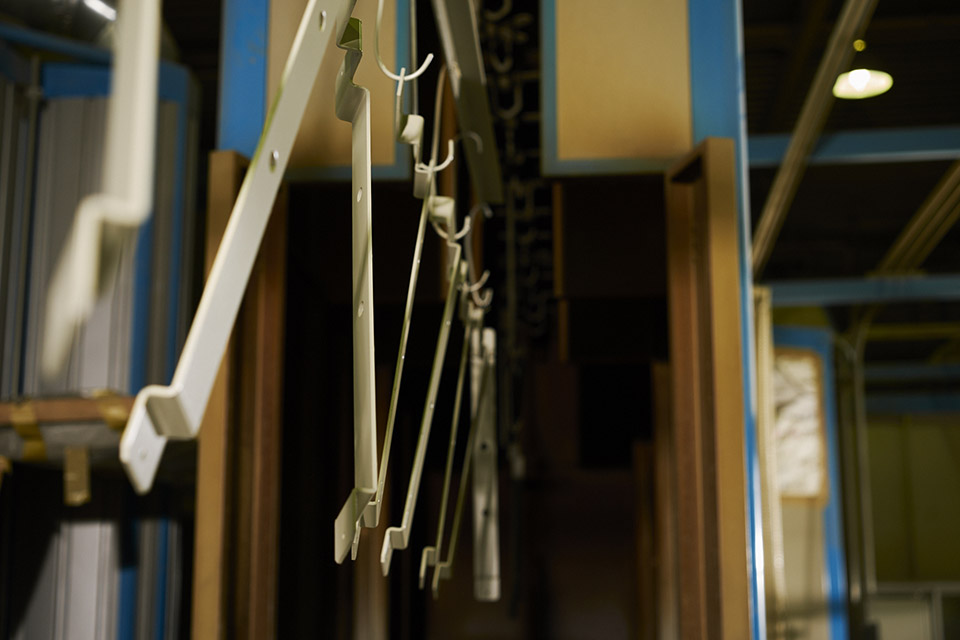
粉体塗装後の乾燥は、溶剤と比較し180~200度と高い温度で乾燥を行います。また乾燥時間で重要となるのは、雰囲気温度ではなく被塗物の温度を規定時間昇温させる必要があることです。このため温度が上がり難い被塗物に関しては、乾燥時間を長くする等の微調整が必要になります。
5. 検査
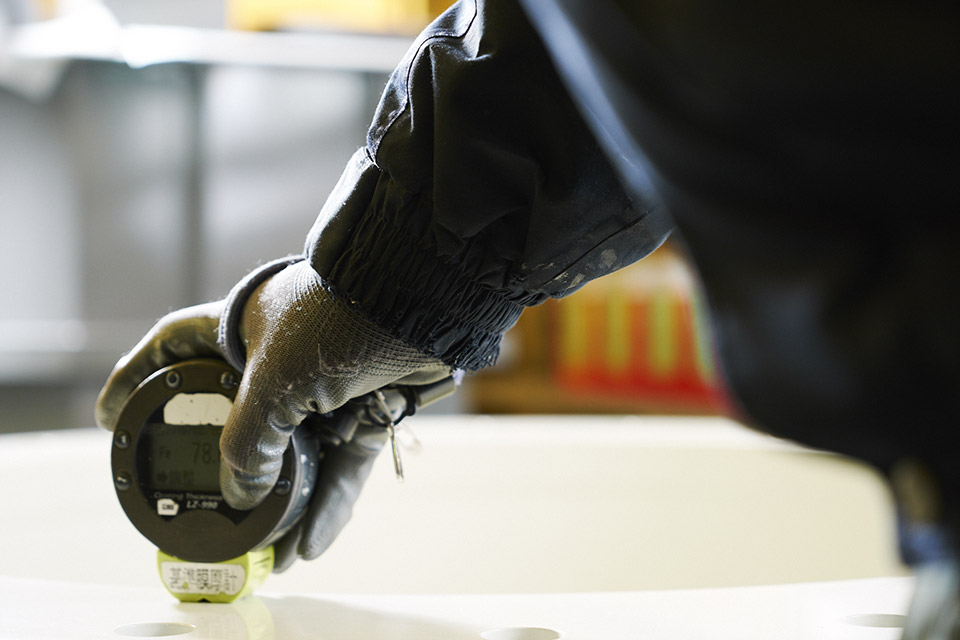
乾燥が完了した被塗物は、出荷前に規定の膜厚、光沢であるか検査を行います。また外観に関しても表面の平滑性、異物の付着、塗り残し等、問題がないか検査を行います。 全ての検査を合格した製品のみ、梱包後にお客様へ納品されます。